- Home
- INSIGHT
- Spare Parts
- What is Driver Blade? Accomplished knowledge in original vs. aftermarket!
What is Driver Blade? Accomplished knowledge in original vs. aftermarket!
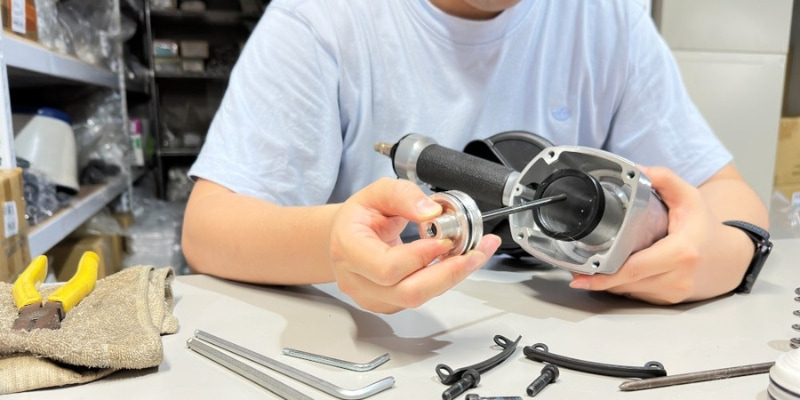
Nowadays, air nail guns are the important tool in fields of construction, carpentry, and renovation. And the driver assembly inside is especially the most indispensable part for nail gun. Whether you are a carpenter engaged in furniture manufacturing or renovation work, a hardware retailer, or even a professional specializing in nail gun repair, you will surely need high-quality piston drivers to replace as it is an easy-wear part. This article will talk about the possible differences between original and aftermarket spare parts.
【Extended reading:All you need to know to choose your perfect air nailers, air staple guns, and air pliers】
What is a piston driver? What are the key components of a pneumatic nail gun?
In a pneumatic nail gun, driver blade is the critical component responsible for driving nails into workpieces. It is typically a cylindrical or rod-like part that is pushed forward upon activation to exert force, striking the nail’s head and driving it into the surface of the workpiece. This action is powered by compressed air, which is released into the nail gun when the trigger is pulled. The piston driver converts the air pressure into mechanical force, propelling the nail quickly and accurately. After each shot, the tool’s remaining air resets the piston and recompresses the air. To put it simply, the driver unit is the "hammer" of the nail gun. It gives the nails the force they need to stay in place.
The piston driver system of a pneumatic nail gun primarily consists of trigger, cylinder, driver blade, bumper, and o-ring, etc. These components work in unison to operate the nail gun. Here's an explanation of the functions of the main components:
- Trigger: The trigger is a crucial component that controls the release of compressed air. When the trigger is activated, it initiates the release of compressed air, driving the entire system. Thus, controlling the timing of air release is crucial for controlling when the driver assembly pushes the nail.
- Cylinder: The cylinder provides space for piston’s movement. The seal of the cylinder directly affects the power and efficiency of the nail gun. When compressed air is released into the cylinder, it pushes the piston forward, creating the thrust that drives the driver blade to fasten the nail.
- Driver Blade (Driver Assembly): When the piston is pushed, the driver blade advances, driving the nails into the surface of the workpiece and securing it.
- Bumper: Located at the top and bottom of the piston, the bumper’s main function is to cushion the impact of the driver assembly's movement, ensuring smooth operation of the nail gun.
Common Specifications for Nail Gun Piston Drivers
The specifications of the driver blade are customized according to the model of the nail gun. Therefore, when choosing a piston driver for your pneumatic nail gun, it's important to make sure the brand and model number of nailer are correct. Otherwise, it might not fit properly with your nail gun, and finally causing assembly issues. If the driver assembly is damaged, it will lead to shallower nail penetration and suboptimal nailing results. Below are common specifications of driver blades that you usually see in the current market.
Types of Driver Assemblies Suitable for Nail Guns
Cross-sectional Shape of the Driver Blade | Types of Nail Guns Suitable for Piston Drivers |
---|---|
![]() |
Coil nailer Concrete nailer Decorative nailer |
![]() |
Framing nailer |
![]() |
Pin nailer Finishing nailer |
![]() |
Carton closing stapler Corrugated nailer Fine wire stapler Narrow crown stapler Wide crown stapler Mattress stapler |
【Extended reading:Understanding Carton Stapler – 4 Points To Choose The Right Tool】
【Extended reading:Everyone Needs to Know the Complete Guide to Wide Crown Staplers】
【Extended reading:6 Points to distinguish Air Pinner and Finishing Nailer - Air Pinner Buying Guide】
【Extended reading:10 Revolutionary Tips for Choosing Coil Nail Guns in Construction】
The Manufacturing Process of the Piston Driver
The manufacturing process of the driver blade for a nail gun typically involves a combination of precision machining and heat treatment. Through these procedures, manufacturers ensure that the piston driver is durable and reliable. This process guarantees that the driver assembly can withstand the demands of frequent use. Below is a description of the production process for driver assemblies, which highlights the critical steps taken to ensure quality and durability. Learn more from video here.
1. Material Selection
The first step in the manufacturing process is selecting the appropriate material for the driver blade and piston, which must have characteristics such as high strength, high temperature resistance, and impact resistance. When producing a piston driver for a nail gun, it's essential to determine the most suitable material based on the specific operational requirements. Otherwise, the driver assembly might potentially lead to operational issues. Below are common materials used for nail gun driver assemblies:
S7
S7 steel material is known for its high impact resistance and toughness, as well as its ease of machining and heat treatment. At moderately high temperatures, it maintains good resistance to softening, making it suitable for applications requiring seismic resistance.
S2
This is an excellent impact-resistant tool steel, featuring outstanding strength and toughness. Its overall performance is exceptional, making it widely used in the manufacturing of high-end tools.
SKD61
SKD61 is a type of hot work tool steel, also known as AISI H13. It's particularly well-suited for making piston drivers due to the following characteristics that repeated impacts and stresses works require: high resistance to thermal fatigue, high toughness, wear resistance, good machinability, and corrosion Resistance. These properties ensure that the piston drivers can withstand the demanding conditions they are subjected to during operation.
DC53
The high wear resistance, excellent toughness, good machinability, high compressive strength, and stable dimensional properties ensures that the piston driver retains its shape and dimensions even after prolonged use. Piston driver will need to remain consistent even under high-stress conditions. Therefore, the stability is essential for maintaining the performance and accuracy of the piston driver over time.
2. Mechanical Processing
Using techniques such as stamping, punching, and forging, the selected material is processed into the required shape and size. Then, fine-tuning methods like milling and turning are used to make the almost-finished product even better by cutting grooves, drilling holes, and making other designs based on specific needs. This manufacturing process ensures that the driver blade has the correct dimensions and shape, allowing for smooth nail driving when the driver blade is installed in the nail gun.
3. Heat Treatment
After machining, the driver blade undergoes heat treatment to enhance its mechanical properties. This typically includes quenching and tempering, which are processes aimed at achieving the desired hardness, toughness, and wear resistance. Through heat treatment, the piston driver is better equipped to withstand the repeated stresses and impacts encountered in nail driving operations. This ensures that the driver assembly can function well under the harsh conditions of driving nails.
4. Surface Treatment
The driver blade's surface treatment during manufacturing may involve sandblasting, blackening, or laser engraving, depending on specific needs. These improvements raise the piston driver's level of recognition in addition to improving its visual appeal. For example, the driver assembly's surface can be further improved in terms of identification by adding particular patterns or marks through laser engraving.
5. Quality Control and Testing
To make sure the driver blade satisfies the necessary requirements and standards, quality control procedures including dimensional checks, hardness tests, and other quality assurance inspections are carried out throughout the manufacturing process. Following the manufacturing process, a nailing test is carried out to verify that the driver assembly and the nail gun are compatible. This test involves loading the driver assemblies into nail guns at random from the same batch and conducting test firings.
Differences between Original and Aftermarket Driver Blades
The main differences between original and aftermarket driver blades lie in price, optional, and compatibility. Original spare parts are of high quality and have excellent compatibility but come at a higher price. In contrast, aftermarket spare parts are less expensive and offer a broader selection of brands. However, their compatibility may vary depending on the supplier, and careful consideration is needed before purchasing. Next, we will explore these differences in more detail.
1. Price Difference
Original driver blade spare parts are generally known for their predictable high quality and guaranteed compatibility, but due to the reputation of the brand and higher maintenance costs, the price of the driver blade is also relatively higher. On the other hand, aftermarket spare parts often come at a lower cost as they save on expenses related to brand marketing, distribution channels, and advertising. This provides a more cost-effective option for users with limited budgets or professional maintenance providers, allowing them to maintain tools at a lower cost.
2. Selection Options
Original driver blade manufacturer typically only offer spare parts of their own brand, which are generally more expensive. If consumers want to purchase parts from multiple brands at once, they must buy from different piston driver manufacturers separately. In contrast, aftermarket spare parts suppliers can provide a variety of driver blade models, including those that are discontinued by the original manufacturers. This allows consumers to purchase all the parts they need in one place and even customize specific piston driver specifications to meet their requirements.
3. Compatibility
Original driver blades are usually fully compatible with specific models of nail guns, as they are manufactured by the same company. The compatibility of aftermarket spare parts can vary depending on the supplier and might have issues such as deviations in machining grooves, or differences in materials, production processes, and part specifications. However, the compatibility and durability of the driver blade with the pneumatic nail gun should be determined by real use.
Comparison chart of Original and Aftermarket Driver Blades
Original Driver Blades | Aftermarket Driver Blades | |
---|---|---|
Price | Higher due to brand reputation and maintenance costs | Lower, more cost-effective |
Quality | Predictable high quality | Can vary depending on supplier |
Compatibility | Excellent, guaranteed for specific models | Varies by manufacturer, often designed to fit well |
Selection Options | Limited to own brand | Wider variety, including discontinued models |
Purchasing | Must buy from different manufacturers for multiple | Can purchase various brands from one supplier |
Aftermarket Driver Blade Manufacturer Recommendation: VIM
VIM offers comprehensive OEM services, producing products according to customers’ requirements, and supplying a variety of driver blade specifications. Our products undergo tens of thousands of in-house inspections, boasting excellent quality comparable to original standards, but at only one-third of the original price! Depending on demand and needed quantity, we can help with spare parts development or with the reproduction of discontinued parts. Among them, theEA0074 driver piston for SENCO SFN40, and TA70278 driver piston for MAX TA551A/16-11 are examples of driver blades that has been discontinued and for which we have successfully provided development assistance.
Conclusion
In the field of aftermarket spare parts manufacturing, VIM has earned the trust of customers with over 20 years of rich experience. We insist on using high quality material, and all products are 100% manufactured in Taiwan, undergoing tens of thousands of rigorous inspections to ensure stable and reliable quality. VIM provides fast and efficient delivery services and offers competitive prices. Do you have a large demand for driver blades or are you looking for a high-quality manufacturer for driver assembly development/production? Feel free to contact us.
Article Classification
Recent Articles
- Need Spare Parts for Paslode Nailers? High Quality Alternatives by VIM
- Stop Downtime: 4 Air Stapler Magazine Issues You Can Solve Today
- 3 Common Magazine Issues in Air Nailers and How to Fix Them
- Air Nailer Troubles? 6 Trigger Issues and How to Fix Them
- What is Driver Blade? Accomplished knowledge in original vs. aftermarket!